Top Guidelines Of Plastic Injection Molding
Wiki Article
Plastic Injection Molding Things To Know Before You Buy
Table of ContentsLittle Known Questions About Plastic Injection Molding.Some Known Facts About Plastic Injection Molding.The 8-Minute Rule for Plastic Injection MoldingThe Ultimate Guide To Plastic Injection Molding
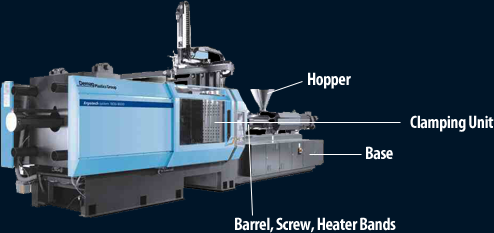
If you intend to discover additionally, the guide covers kinds of mould tools, along with special ending up processes such as colours & plating. Words that are underlined can be discovered in the glossary in the appendix ... Part I: Moulding: The Essentials The Advantages of Shot Moulding Plastic injection moulding is an extremely precise process that offers a number of benefits over other plastic handling methods.
Precision is excellent for extremely detailed parts. Compared to other strategies, moulding permits you to include more attributes at really little tolerances. Have an appearance at the image to the. You can hold this moulding in the palm of your hand and also it has bosses, ribs, steel inserts, side cores and also holes, made with a moving closed off attribute in the mould tool.
Utilizing a UK moulder with existing connections to China can eliminate the threat as well as still result in cost-saving ... Cavity - The component of an injection mould tool that offers the plastic product its form, that does the real moulding of the plastic. See mould tool phase on pages 5 and also 6 for all terms associated with the mould device Cycle time - The time it takes for a mould cycle to be finished, i.
from material feed & melting; material injectionProduct shot time cooling down ejection and also the re-closing of the mould tool ready device the next cycleFollowing Draft angles - The walls of a moulded part need to be somewhat tapered in the instructions in which the component is ejected from the mould tool, to permit the component to be expelled easily (plastic injection molding).
Ejector stroke - The pushing out of ejector pins to expel the moulded component from the mould device. Ejector stroke speed, size and timing requires to be carefully managed to avoid damage to the ejectors as well as mould device, yet at the same time make the moulding cycle as short as possible.
4 Easy Facts About Plastic Injection Molding Shown
Overlocking - When a mould tool has been established right into a moulding equipment inaccurately, creating the device to close as well difficult as well as so harmful the mould tool Part repeatability - The ability to develop similar plastic components time after time Span - Perfectly straight edges are difficult to eject from the mould tool.Ribs - When a plastic part has thin walls, ribs are contributed to the layout to make the slim wall surfaces stronger Side cores - Side action which produces a feature on a moulded component, at an opposing angle to the typical opening direction of the mould device. The side core requires to be able to pull back as the plastic part can not be expelled or else.
Walls - The sides of a moulded part The message on this page is a sample from our complete White Paper 'Injection Moulding for Buyers'.
Production procedure for producing components by infusing liquified material into a mould, or mold and mildew Streamlined diagram of the procedure Shot moulding (U.S. punctuation: injection molding) is a manufacturing procedure for creating components by injecting molten product into a mould, or mold and mildew. Injection moulding can be performed with a host of materials generally including steels (for which the process is called die-casting), glasses, elastomers, confections, and the majority of frequently thermoplastic and thermosetting polymers. Injection moulding is extensively used for making a variety of parts, from the tiniest components to entire body panels of autos. Injection moulding utilizes a special-purpose equipment that has 3 components: the injection her comment is here system, the mould as well as the clamp.
5 Simple Techniques For Plastic Injection Molding
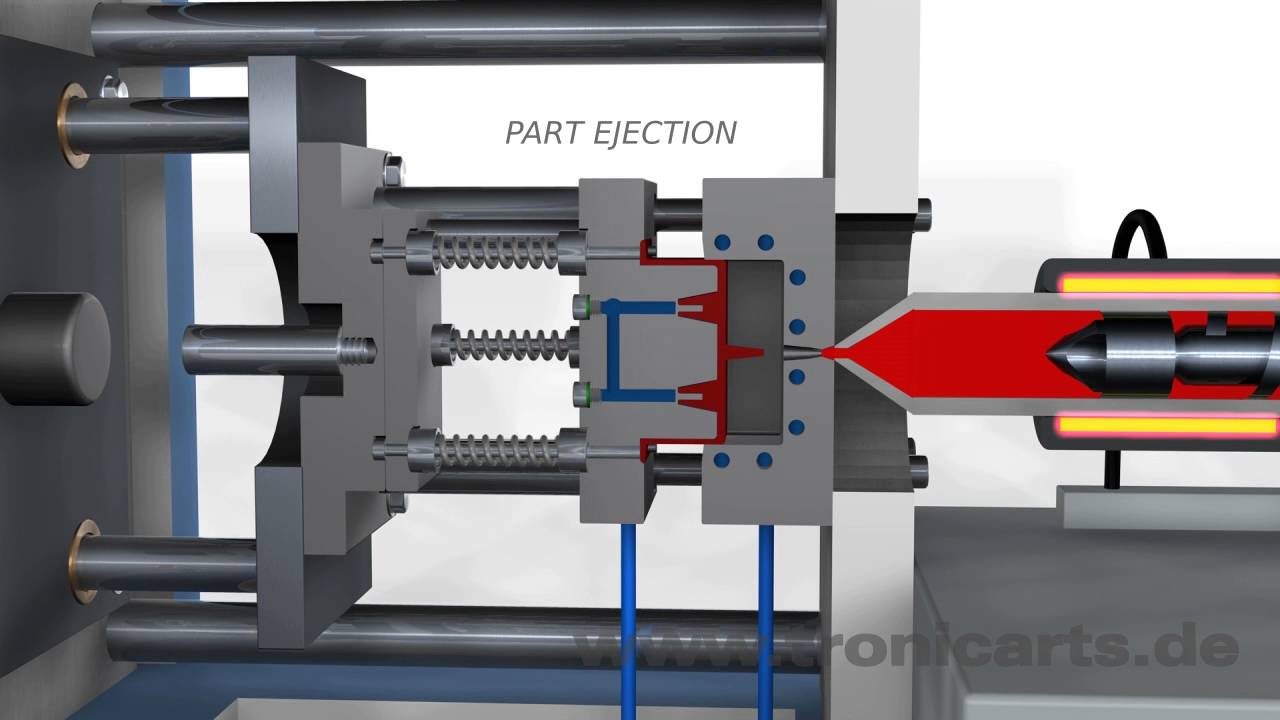
In multiple dental caries moulds, each cavity can be the same and develop the same parts or can be unique as well as develop numerous different geometries throughout a solitary cycle.
When enough material has gathered, the material is required at high pressure as well as speed right into the component creating cavity. The exact amount of shrinkage is a function of the resin being used, and can be relatively predictable. To avoid spikes in pressure, the process typically utilizes a transfer setting corresponding to a 9598% full cavity where the screw shifts from a constant rate to a consistent stress control.
As soon as the screw gets to the transfer setting the packing pressure is applied, which finishes mould dental filling as well as compensates for thermal shrinking, which is quite high for thermoplastics relative to many various other products. The packing pressure is used till the gateway (cavity entrance) solidifies. Because their explanation of its small size, the gateway is usually the top place to solidify through its entire thickness.: 16 Once eviction strengthens, say goodbye to product can get in the tooth cavity; as necessary, the screw reciprocates and also acquires material for the next cycle while the product within the mould cools down so that it can be ejected as well as be dimensionally secure.
Report this wiki page